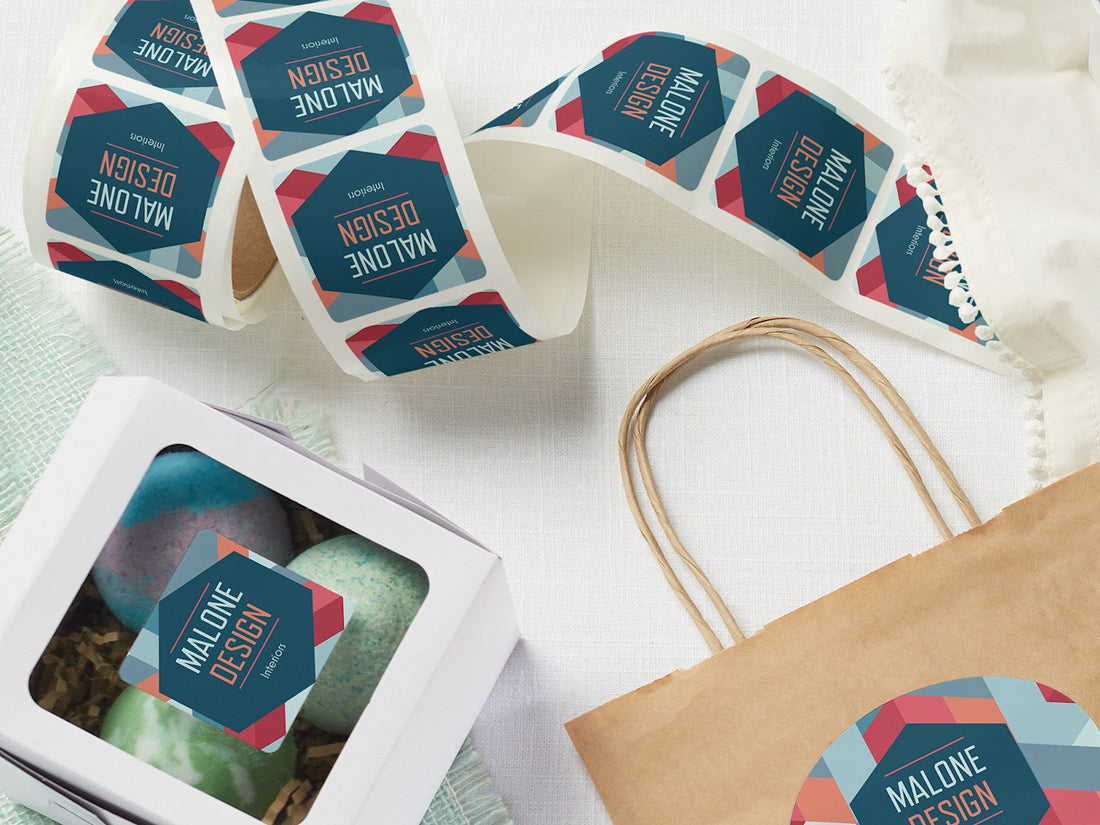
How Flexography Works: A Deep Dive into Printing Techniques
Share
Understanding how flexography works is crucial for tech professionals and enthusiasts alike, especially those involved in the printing and packaging industry. This printing technique has gained immense popularity due to its **speed**, **versatility**, and **high-quality output**. In an era where efficiency is key, flexography stands out as a game-changer.
Flexography is a form of rotary printing that utilizes flexible relief plates. It is primarily used for printing on a range of substrates, including plastic, film, metallic films, and paper. The method is particularly effective for packaging applications, where **bold**, **vibrant colors** and **sharp images** are essential for consumer appeal.
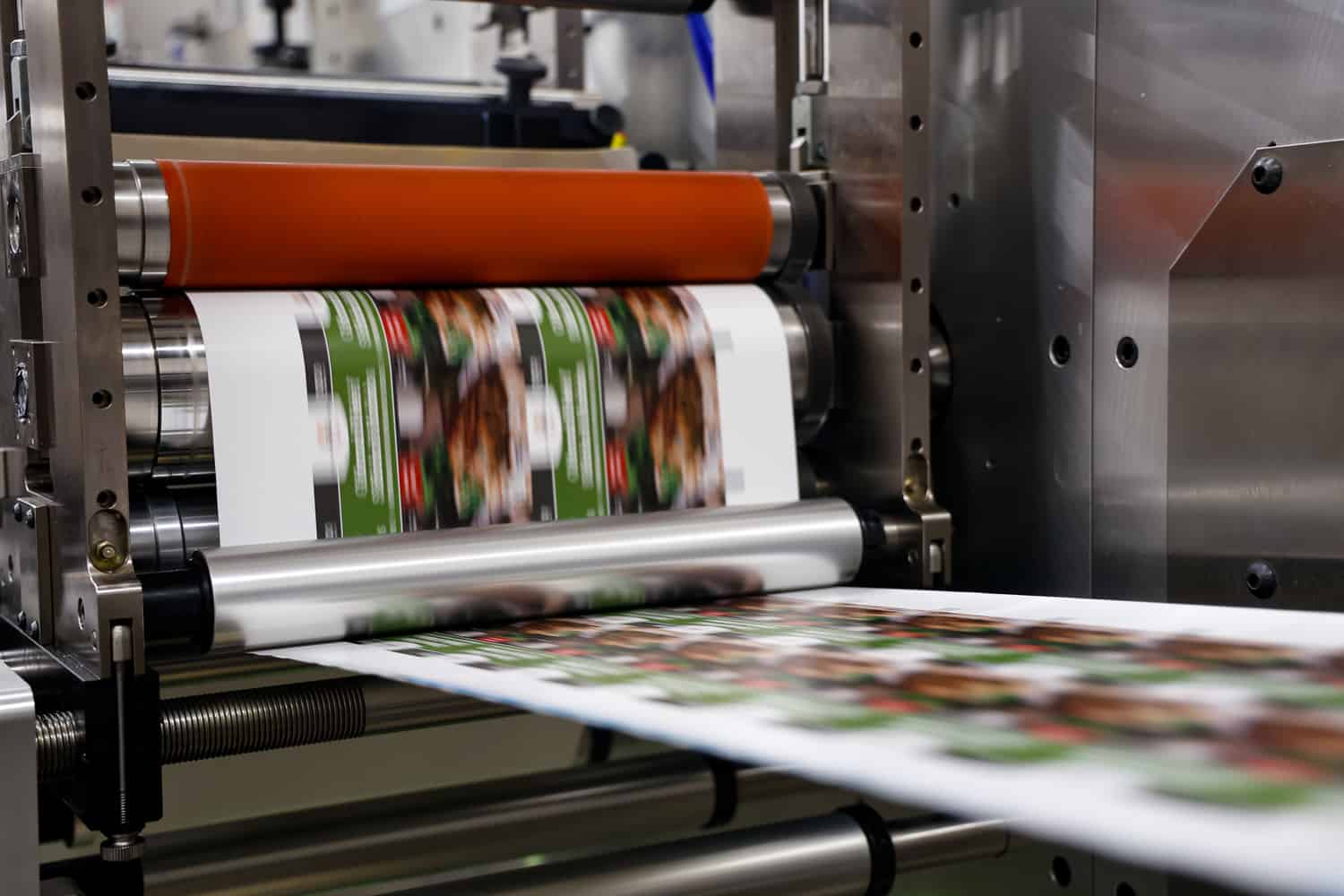
The Mechanics of Flexographic Printing
First off, lets delve into the process that forms the backbone of flexography. In this printing method, ink is transferred to the substrate through a series of steps:
- Plate Preparation: Flexographic printing begins with the creation of the image on a photopolymer plate. This plate is made from flexible material, allowing it to adapt to various surfaces.
- Ink Transfer: The ink is applied to the raised surface of the plate, with the excess ink being removed, ensuring a smooth transfer.
- Substrate Feeding: The substrate, such as paper or plastic, is continuously fed through the press, allowing for high-speed printing.
- Drying: After the ink is applied, it is dried using either hot air or UV light, solidifying the image on the substrate.
Benefits of Flexography
Understanding how flexography works reveals the numerous benefits that make it a preferred choice for many businesses:
- Speed: Flexo presses can operate at high speeds, producing thousands of prints per hour.
- Versatility: This method can print on various surfaces, including irregularly shaped items.
- Cost-Effective: Flexography reduces ink usage compared to traditional methods, lowering production costs.
- Environmental Consideration: Water-based inks can be used, making it a more eco-friendly option.
Applications of Flexography
Flexography is used in multiple applications across various industries. Here are some key areas:
- Packaging: Food, beverage, and product packaging consistently utilize flexographic printing for eye-catching labels.
- Labeling: Flexo is prevalent in the production of labels for bottles, containers, and jars, as its high-speed capabilities meet market demands. You can learn more about making labels in Word.
- Newspapers and Magazines: Flexographic printing is known for its ability to produce high-quality graphics for publications.
Common Issues in Flexographic Printing
Even though flexography is superior, it is not without its challenges. Some common issues include:
- Ink Transfer Problems: Improper ink viscosity can lead to inconsistent printing.
- Plate Wear: Over time, the printing plates can wear down and affect print quality.
- Drying Issues: Insufficient drying can lead to smudging or rubbing off of ink.
Recent Innovations in Flexography
With technology evolving, so does flexography. New techniques and technologies are emerging:
- Digital Flexography: Integrating digital technology allows for better control and faster adjustments.
- Automation: Automated systems are improving production speeds and reducing setup times.
Recent Trends and Future of Flexography
As industries seek sustainability, flexography is adapting to ensure it meets these demands. The future looks promising as manufacturers focus on:
- Eco-friendly Inks: This trend will likely continue to grow as environmental impact becomes a crucial factor.
- Integration with Digital Processes: The combination of traditional flexography with digital workflows offers greater flexibility and efficiency.
FAQs
- What is flexography?
- Flexography is a modern printing technique that uses flexible relief plates to transfer ink onto a variety of substrates.
- Where is flexography commonly used?
- It is primarily used in packaging, labeling, and producing special publications.
- What are the benefits of using flexography?
- Flexography offers speed, versatility, cost-effectiveness, and eco-friendliness.
As an Amazon Associate, I earn from qualifying purchases.