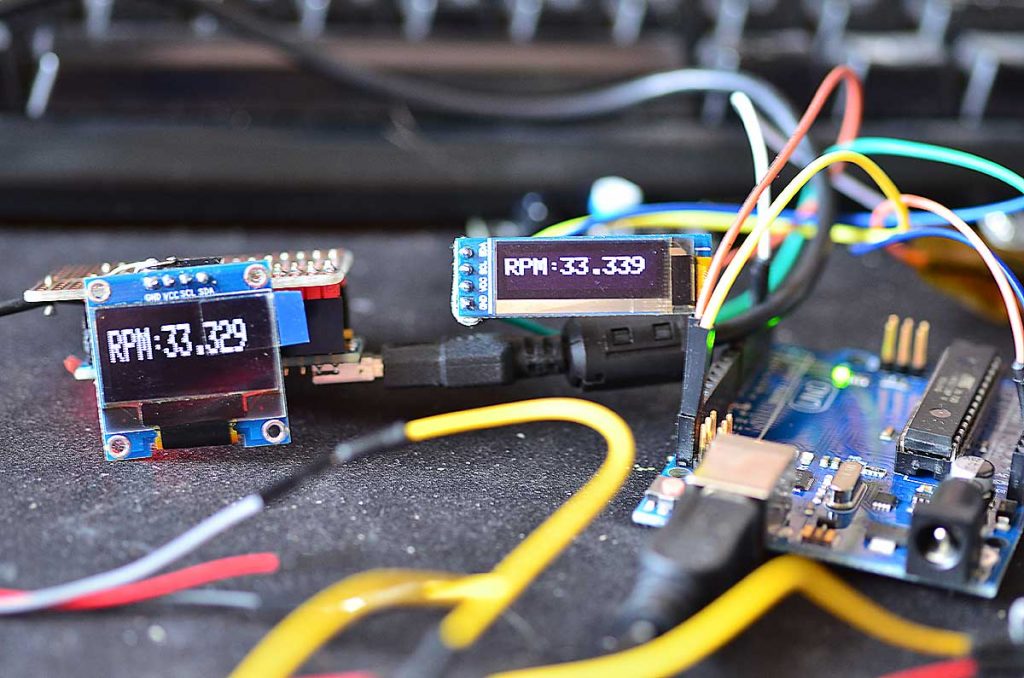
How Does a Digital Tachometer Work? Shocking Life-Changing Tech
Share
In the world of engineering and automotive technology, understanding how a digital tachometer works is essential for tech professionals and enthusiasts alike. This remarkable device not only measures engine speed but also plays a vital role in improving vehicle performance. In this article, we will dive into the intricacies of digital tachometers, exploring their components, working principles, and the cutting-edge technology that powers them.
The digital tachometer is a crucial tool that provides real-time feedback to the operator, allowing for precise control over engine performance. For those asking, how does a digital tachometer work, we will break down its operation step by step.

The Basics of a Tachometer
A tachometer is an instrument used to measure the rotational speed of a shaft or disk, most commonly found in engines. The term is derived from the Greek words 'tachos,' meaning speed, and 'metron,' meaning measure. Traditionally, tachometers were mechanical devices that relied on physical components. However, with advancements in technology, digital tachometers have become increasingly prevalent due to their accuracy and reliability.
Key Components of a Digital Tachometer
Understanding the components of a digital tachometer is essential to get a better grasp of how it functions. Here are the key elements involved:
- Sensor: This is the heart of a digital tachometer. Sensors, such as inductive or Hall-effect sensors, detect the rotational speed of the engine's crankshaft. They convert mechanical movement into an electrical signal.
- Microcontroller: The microcontroller processes the signals received from the sensor, applying algorithms to calculate the RPM accurately.
- Display: A digital screen presents the RPM readings to the user in a clear and easy-to-read format.
- Power Supply: Digital tachometers require a power source, which can be from the vehicle's electrical system or an external battery.
How Digital Tachometers Measure RPM
Now that we understand the key components, lets delve into how these devices measure RPM:
- **Signal Generation:** The sensor detects the rotational speed of the engine and generates a signal, often in the form of a voltage or pulse output.
- Signal Processing: The microcontroller processes the incoming signals to determine the rate of rotation effectively.
- Display Output: Finally, the processed information is displayed on the digital screen, thus giving the operator real-time insights into the engine's performance.
The Technology Behind Digital Tachometers
The advancement of technology has improved the accuracy and functionality of digital tachometers. Some of the most significant innovations include:
- Data Logging: Many modern tachometers provide data logging features that allow users to record RPM over time for analysis.
- Integration with Other Systems: Digital tachometers can now be integrated with other systems, such as OBD-II and engine management systems, for enhanced vehicle diagnostics.
- Tunable Outputs: In performance vehicles, tachometers can be tuned to provide specific outputs for modifications made to the engine.
Applications of Digital Tachometers
Digital tachometers have a wide array of applications across various fields:
- Automotive: Used extensively in cars, trucks, and motorcycles to monitor engine performance.
- Aviation: Essential for monitoring aircraft engine RPM, ensuring safe operation.
- Industrial Machines: Employed in manufacturing facilities to monitor the speed of motors and turbines.
Advantages Over Mechanical Tachometers
While mechanical tachometers have served their purpose over the years, digital tachometers present several advantages:
- Accuracy: Digital tachometers provide real-time, high-precision RPM readings.
- Visual Display: Clear digital displays make it easier for users to read and interpret data quickly.
- Less Maintenance: Digital devices require significantly lower maintenance compared to mechanical ones.
Conclusion
In summary, understanding how does a digital tachometer work can significantly enhance performance monitoring and operational efficiency. These devices are revolutionizing how engineers and mechanics interact with engines, offering features that empower professionals to optimize performance. From the basic functioning to advanced technological integrations, digital tachometers are indeed a terrific advancement in measurement technology.
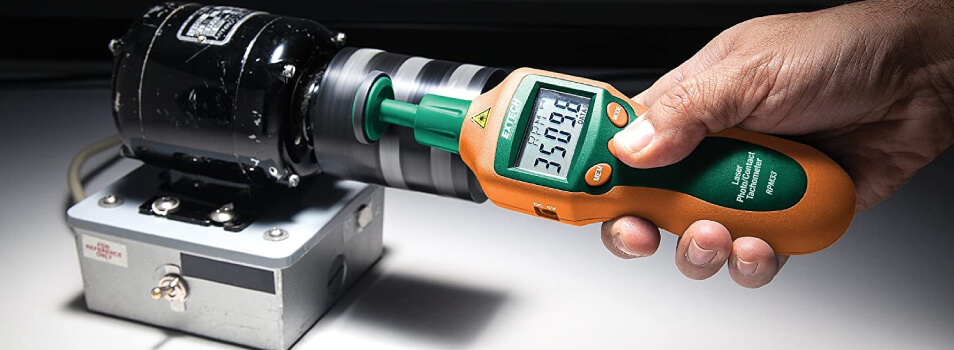
Frequently Asked Questions
1. What is the difference between analog and digital tachometers?
Digital tachometers provide precise RPM readings through electronic sensors, while analog tachometers use needles and mechanical components, which can be less accurate.
2. Can a digital tachometer be used for any engine type?
Yes, digital tachometers can be calibrated for various engine types, including gasoline, diesel, and electric engines.
3. How do I troubleshoot a faulty tachometer?
Check the wiring, replace any defective sensors, and ensure the device is properly calibrated to troubleshoot issues with a tachometer.
For more on the subject, you can read about how to wire a tachometer or learn about tachometers in historical contexts.
Understanding digital tachometers has never been so vital. Dont miss this opportunity to evolve your knowledge in this crucial field of technology!